Böttcher Developments: Innovative. Flexible. First-Class. Worldwide.
With Böttcher products, you benefit from years of intensive development - the results of which are optimized to meet the needs of specific applications. No matter where industrial rollers are used - our materials offer outstanding hardness and dimensional stability as well as excellent application and transfer characteristics combined with optimum elasticity. Böttcher coverings also ensure optimum edge-cut resistance and a high degree of cut and abrasion resistance, thus reducing grinding cycles accordingly. You benefit from longer machine service life, lower setup costs and - above all - optimum process results with excellent production reliability.
Roller coverings produced using the ribbon-flow process offer key advantages. The need to dismantle bearings and other accessories is eliminated, thus increasing the speed and flexibility of production processes. And that is why we continue to explore the potential offered by this method for all industrial applications. We are presently working with 20 tested and proven materials covering a broad range of hardnesses from 50 to 100 Shore A.
Roller coverings used in the plastics, metal, wood and textile industries are subject to particularly demanding requirements. We meet these requirements with individualized solutions that offer you more quality, economy and
Our compounds (PDF, 1418 kB)
Our Compound overview 1 MB
Auszug aus unserer Werkstoffpalette. Physikalische Eigenschaften. Chemische Beständigkeit.
- Excellent hardness and dimensional stability
- Outstanding application and transfer characteristics
- Excellent physical properties
- Optimum elasticity
- Ribbon-flow coverings in hardness grades from 50 to 100 Shore A
Special materials with optimum dynamic properties, edge-cut and infeed-cut resistance for aluminium rolling mills
Ribbon-flow materials:
- heat-resistant for heavy duty S-rolls in proximity to the furnace
- hydrolysis-insensitive coverings for squeeze rolls in back-endsqueeze units
- optimum homogeneity for varnishing rollers in coil-coating units
- Lackierwalzen mit Sleeve-Technologie
- Moosgummiwalzen für Beizen Lackier- und Leimwalzen für den Veredelungsprozess
- Viton- und Silikonbeschichtungen
- Anti-static polyurethane materials
- Temperature resistant polyurethane materials
- special materials designed to ensure maximum squeezing performance under extreme thermal and mechanical load conditions along web edges
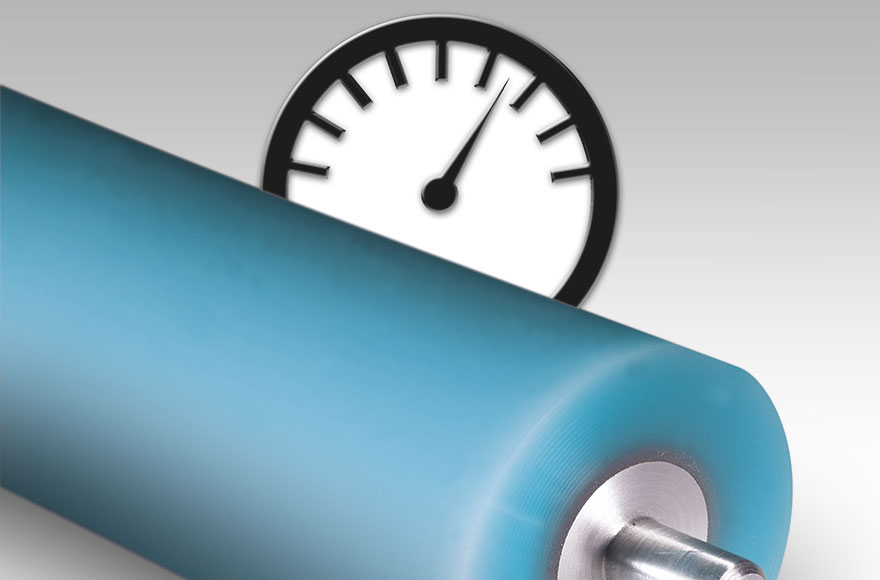